レーザー加工機を使うと、材料によっては排気が大変
レーザー加工機beamoはA4サイズまでの加工ができるデスクトップレーザー加工機。
我が家に来てからというもの、ものづくりが楽しくてさまざまな素材を試行錯誤しています。最初は木材を加工していたのですが、最近ではアクリルなどの樹脂などにも幅が広がり、加工の経験値も少しずつ上がってきました。
そんな中、特にアクリルやエコラバーなどを加工したときの臭いがものすごく、場合によっては頭が痛くなるレベル。レーザー加工機の加工NG素材にはなっていないけど、きっと身体にはよくない臭いなんだろうな・・・と思っています。
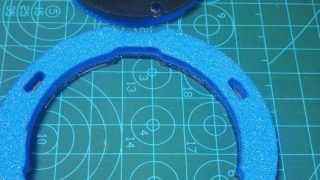
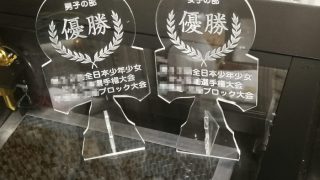
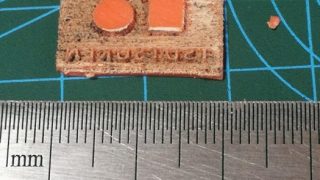
beamoは6畳間の1室に置いているので、使うときは窓を開けてFilter(beamoオプション)の出口を外に向けていました。(なんだか「家政婦は見た!」みたいに見えるFilterくん)
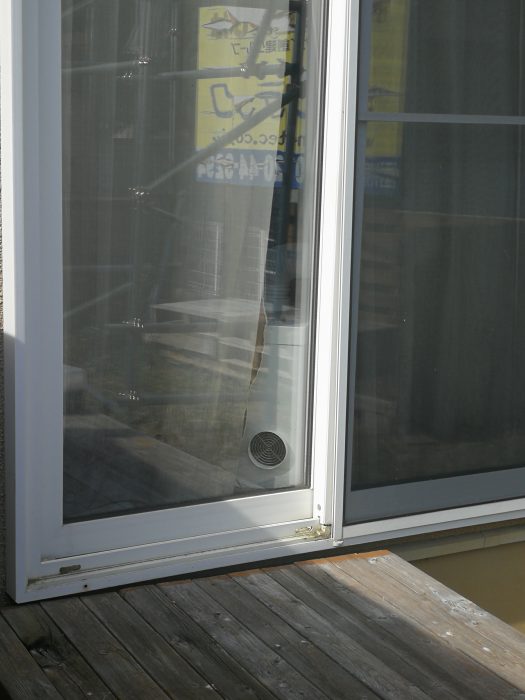
ちなみにガラスにほんのりと映っている単管を組み合わせたものはSASUKEね。
https://zukutora.com/handmade/sasuke1
窓を開けているだけだと、当然風向き次第では排気がそのまま部屋に戻ってくる結果となり、とても臭い。そしてこれからの季節は冬。窓を開けると信州の冬は寒くて仕方がないわけです。
どうにか対策をしないと・・・と思っていて、ようやくダクト用の窓を作ることを決意しました。
ダクト用窓づくり
今回は1×4材を使い、窓の大きさにあわせて四角く組み、両側にポリカの透明板0.5t(いただきもの)を貼ってみました。
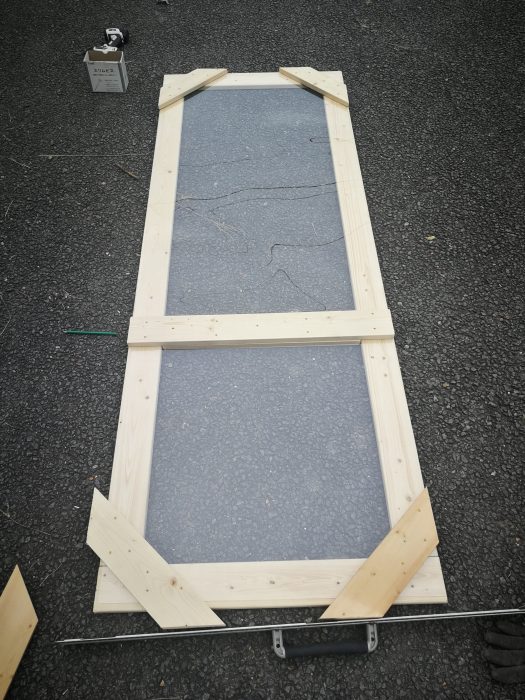
窓にはめてみたところ、一応ピッタリできてるんじゃない??
しかしここで痛恨のミス!ポリカの板を枠にピッタリと固定するのを忘れてしまった!!
両面テープで隙間をふさがないとそこから臭いも入るし、虫も入るよね。
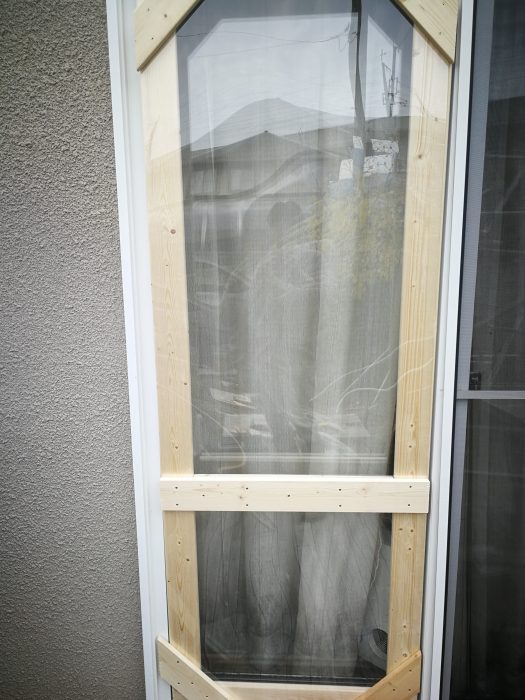
とりあえずビスを緩めつつあとから手が入る範囲で両面テープ止めをしてみました。段取りとても大事。なお、外周に隙間がどうしてもできるので、隙間テープを外周に貼ってはめてみたところ、しっかりハマりました。
ダクト穴の加工
手作りした窓に、ダクト穴を開ける必要があります。
どうやって丸く切ろうかと考えて、アクリルをbeamoで丸くそのサイズにカットし、当てて切る作戦をとりました。
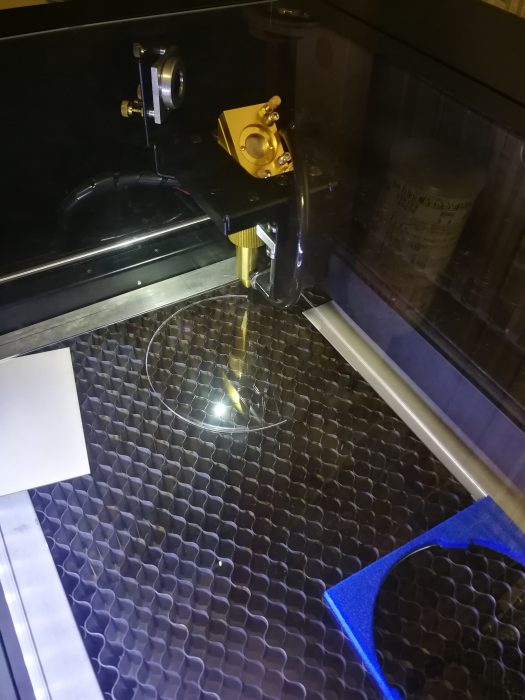
丸く切ったアクリルを当てます。これがカッターのガイドになります。
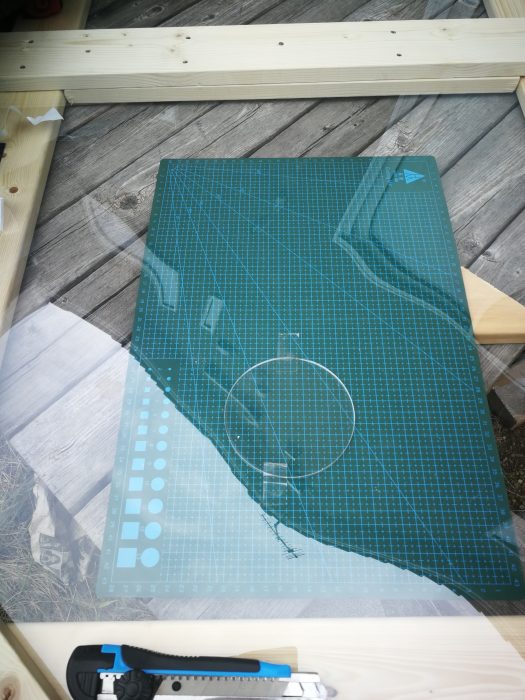
結構キレイに丸く切れたんじゃない??
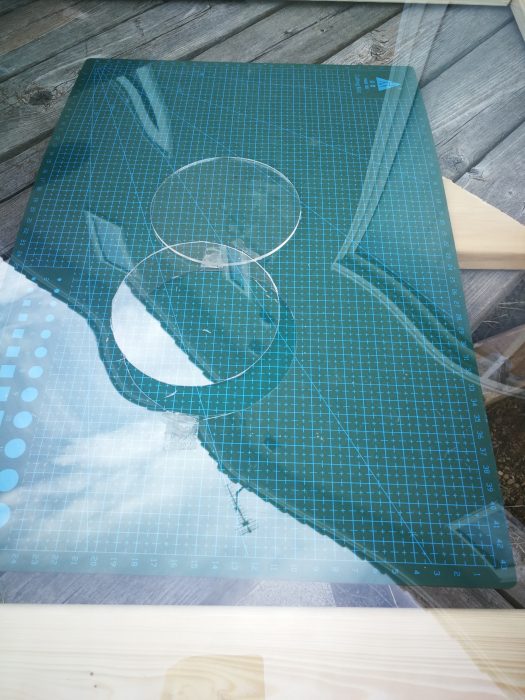
ダクトを通してみたらピッタリ!!でもここで続いての痛恨のミス!!
ダクト穴の位置を全然考えていなかったら、高さが全く違うw
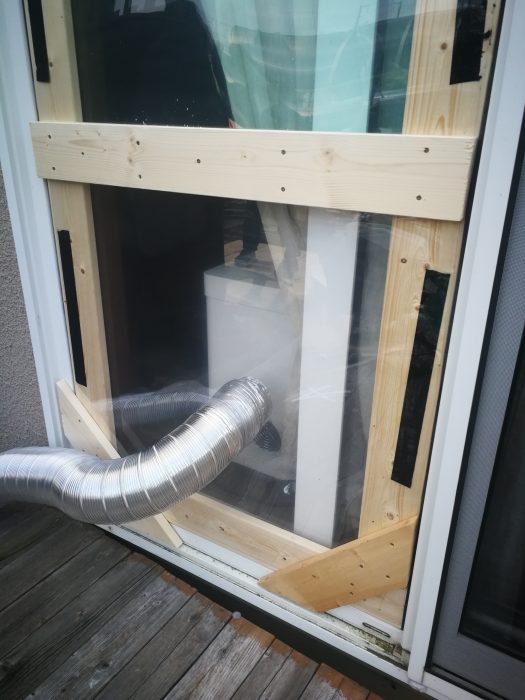
急遽beamoの下にゲタを履かせることにし、高さをあわせて台座をつくり、Filterと連結完了。
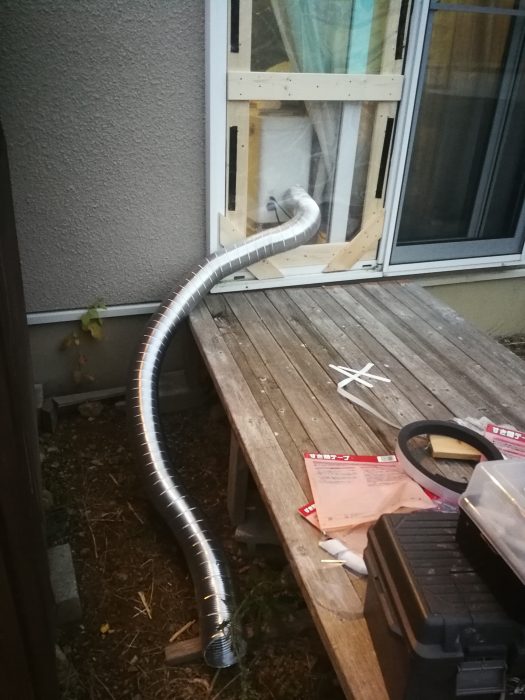
ところがbeamoの使用が終わって、元々の窓を閉める際にダクトが邪魔になることが判明。さらに設計変更をしてみました。
連結部分の造作
ダクトの連結部は取り外しができるようにし、必要に応じて窓を開けたり閉めたりできる構造にしたい。
そこで連結パイプを取り付けて、室内は着脱可能に作り直すことにしました。
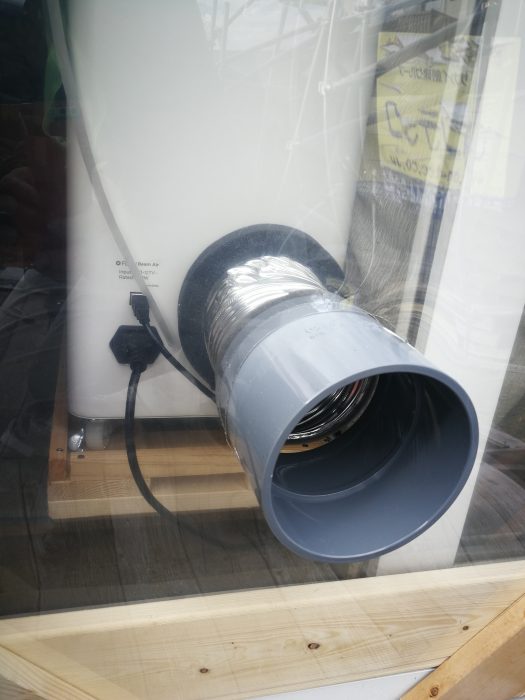
先にアクリルを当ててカットした部分をさらに広げたので、アクリルが無駄になったw
このままアルミフレキパイプを挿入すると、隙間ができるのでフレキパイプの周囲には隙間テープを貼りました。
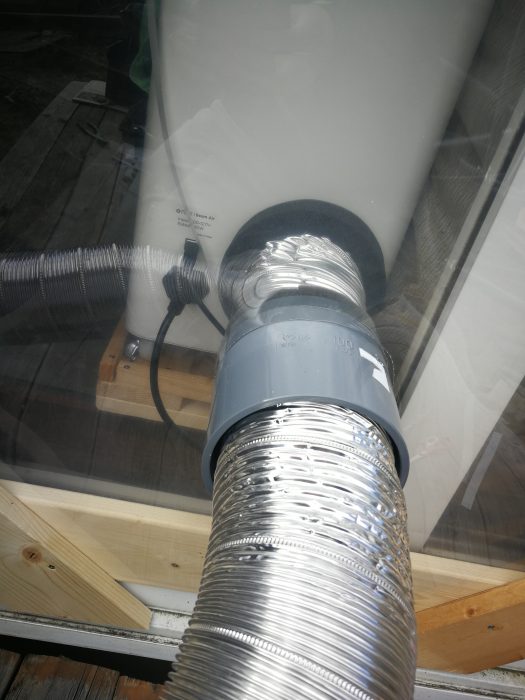
隙間テープを連結部に貼ってあげることでこんなにもいい感じに接続できるとは思わなんだ。
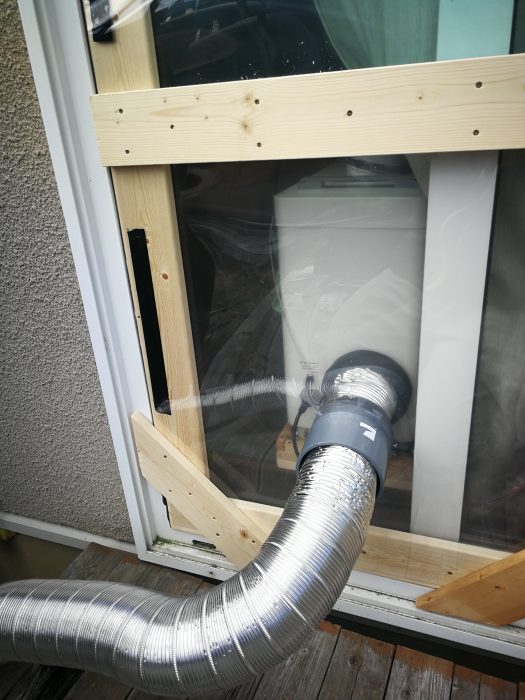
排気が漏れそうな場所には隙間テープ。窓を開けて、Filterと連結するときはこんな感じ。
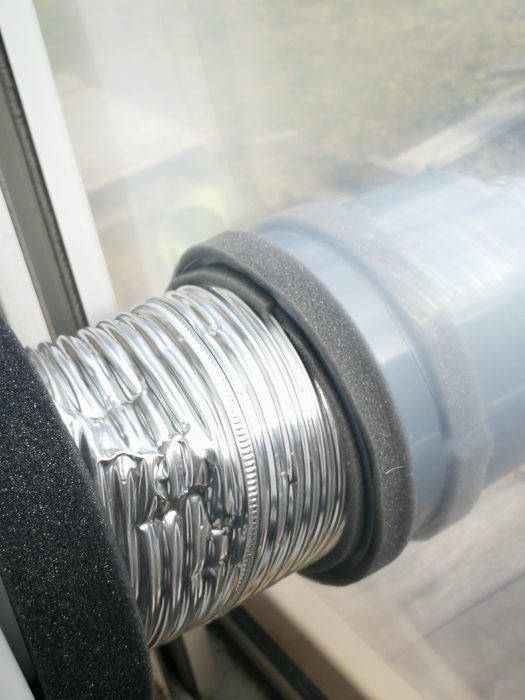
beamoを使い終わったら、フレキパイプを離して窓を閉めます。
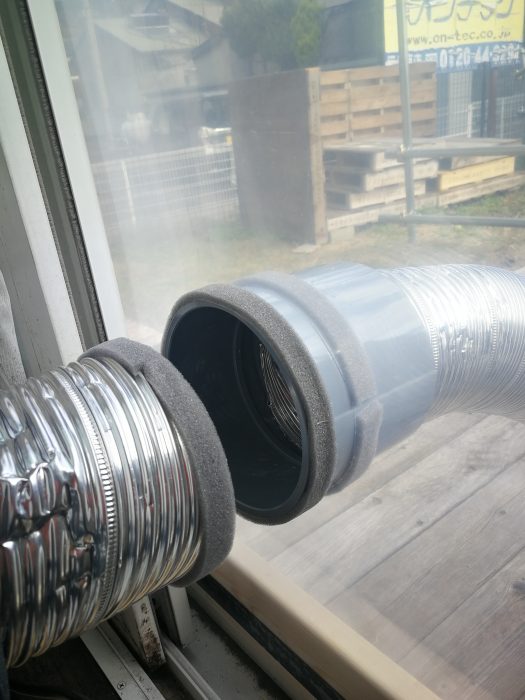
使い心地がとてもいい
実際にこれで運用してみたところ、お世辞抜きにとてもいい。
・臭いが部屋の中に籠らない
・寒くない
思ったとおりの結果が得られて、これで冬でも気兼ねなくレーザー加工を楽しめそうです。
ちょっとしたDIYでしたが、やっただけの効果は十分!見栄えは正直あんまりよくないけどww
外から簡単には目につく場所ではないので、しばらくこれで運用してみたいと思います。

にほんブログ村